Unlocking the Potential of Plastics Molding in Metal Fabrication
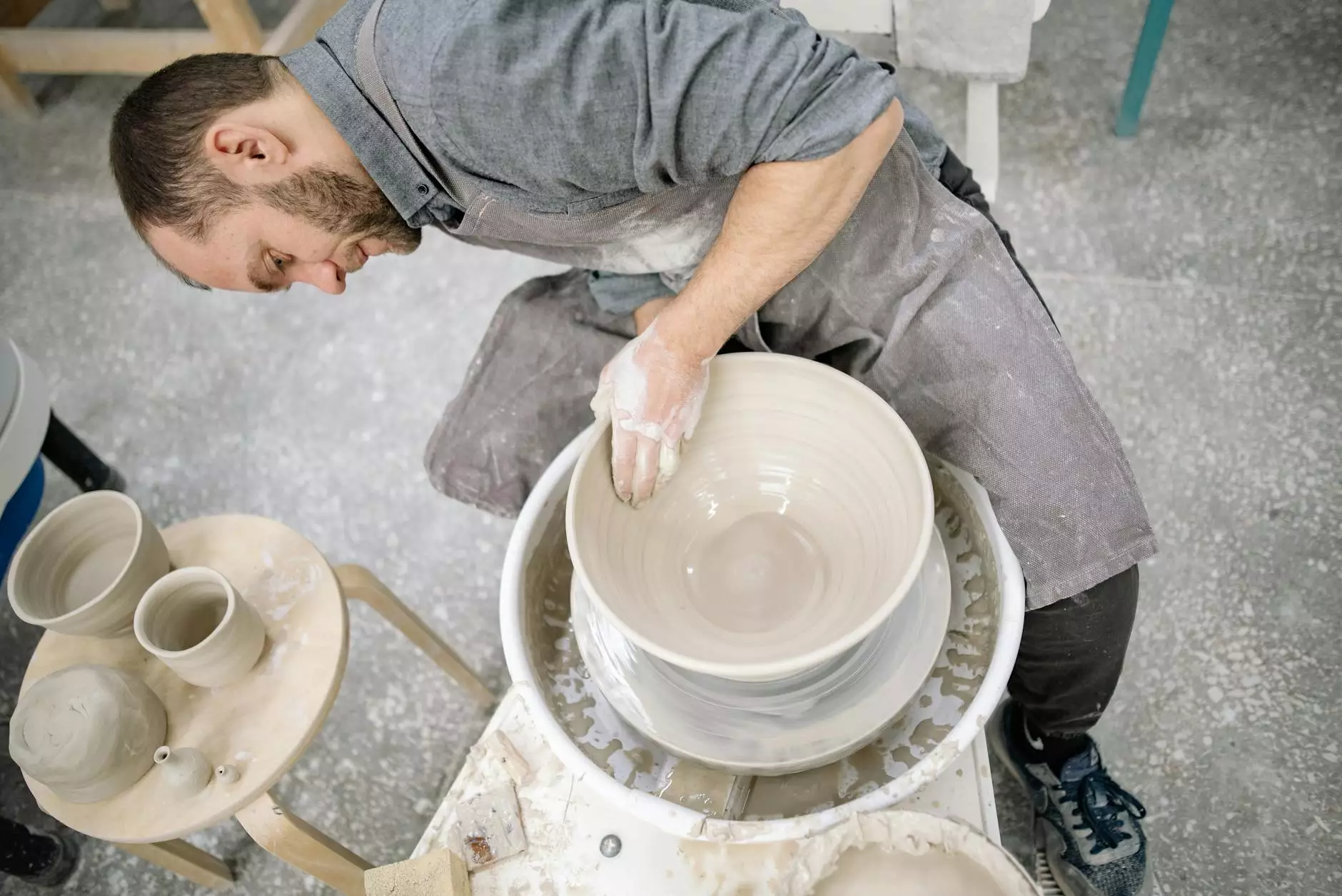
The world of plastics molding is vast and intricate, yet it offers incredible opportunities, especially when paired with traditional manufacturing methods like metal fabrication. As industries continue to evolve, understanding the synergy between these two realms is crucial for business owners, engineers, and entrepreneurs looking to streamline production and enhance product quality.
Understanding Plastics Molding
At its core, plastics molding refers to a manufacturing process used to produce parts by injecting molten plastic into a mold. This technique has revolutionized the production capabilities across various sectors, providing remarkable efficiency, versatility, and cost-effectiveness. Below are some key methodologies involved in plastics molding:
- Injection Molding: The most common method where thermoplastic materials are melted and injected into a mold under high pressure.
- Blow Molding: Used primarily for hollow plastic products, this process involves inflating hot plastic to form containers and bottles.
- Compression Molding: A method suitable for thermosetting plastics, where a preheated plastic charge is placed into a mold cavity and then compressed.
- Rotational Molding: This technique is ideal for creating large plastic products. It involves heating a hollow mold filled with powdered plastic, which coats the interior as it rotates.
The Intersection of Plastics Molding and Metal Fabrication
In the realm of metal fabrication, the incorporation of plastics molding opens new avenues for innovation. Here are a few ways these two manufacturing processes interact:
1. Cost Reduction
By using plastics as components in metal products, companies can significantly reduce weight and costs. For instance, incorporating plastic parts in assemblies traditionally made entirely of metal can lead to savings in material costs and energy consumption during transport.
2. Enhanced Product Features
Plastics molding allows for the creation of complex shapes and features that might be challenging or impossible to achieve with metal alone. This capability leads to products that are not only innovative but also perform better in certain applications.
3. Streamlined Production Processes
The integration of plastic components can streamline production timelines. For instance, using plastic enclosures for electronic components reduces the need for additional machining typically required in metal parts.
Applications of Plastics Molding in Metal Fabrication
The applications for plastics molding in the context of metal fabrication are broad and diverse, impacting a variety of industries:
- Automotive Industry: In automotive manufacturing, plastic components such as dashboards, panels, and housings often complement metal structures.
- Aerospace: Weight reduction is critical in aerospace. Using plastics for interior components alongside metal frameworks can lead to improved fuel efficiency.
- Electronics: The casing for electronic devices frequently applies plastics molding techniques, offering lightweight and durable solutions.
- Consumer Goods: Many household items combine metals and plastics, enhancing usability and aesthetics.
The Benefits of Plastics Molding
The benefits of adopting plastics molding are numerous and can lead to significant improvements in production lines and product outcomes:
1. Design Flexibility
With modern plastics molding technologies, designers can easily create intricate designs that meet both aesthetic and functional requirements.
2. Longevity and Durability
Plastics can enhance the longevity of products. Many modern plastics offer resistance to factors such as corrosion, moisture, and chemicals, making them ideal for various applications.
3. Sustainability
With the push toward sustainability, many manufacturers are now producing biodegradable plastics or utilizing recycled materials in their plastics molding processes. This commitment to sustainability not only helps the planet but also appeals to environmentally conscious consumers.
Challenges in Plastics Molding
Despite its advantages, plastics molding does come with challenges that need to be navigated carefully:
- Material Limitations: Not all plastics can withstand the same temperatures and pressures as metal, which can limit their use in certain high-performance applications.
- Quality Control: Ensuring the quality of plastic components can be challenging. Variability in molding processes can result in defects that require additional inspection and testing.
- Environmental Concerns: While advances are being made in sustainable plastics, traditional plastics still face scrutiny regarding their environmental impact.
The Future of Plastics Molding and Metal Fabrication
The future of plastics molding within metal fabrication looks promising, driven by advancements in technology and materials science. Some key trends to watch include:
1. Advanced Materials
Innovations in material science are leading to the development of high-performance plastics that can withstand extreme conditions, making them ideal candidates for critical applications in metal fabrication.
2. Increased Automation
The rise of Industry 4.0 means that more companies are implementing automation in their manufacturing processes, which can improve efficiency and reduce waste in both plastics molding and metal fabrication.
3. Collaborative Manufacturing
As the lines between plastics molding and metal fabrication continue to blur, collaborations between designers, engineers, and manufacturers will become more common, leading to innovative products that leverage the strengths of both materials.
Conclusion
In conclusion, the integration of plastics molding within the metal fabrication industry is transforming the way products are designed, produced, and marketed. As businesses like deepmould.net adapt to these trends, those who embrace this synergy will undoubtedly find themselves at the forefront of innovation, efficiency, and sustainability in manufacturing. By understanding the advantages, challenges, and future implications of this combination, companies can strategically position themselves to thrive in an ever-evolving marketplace.